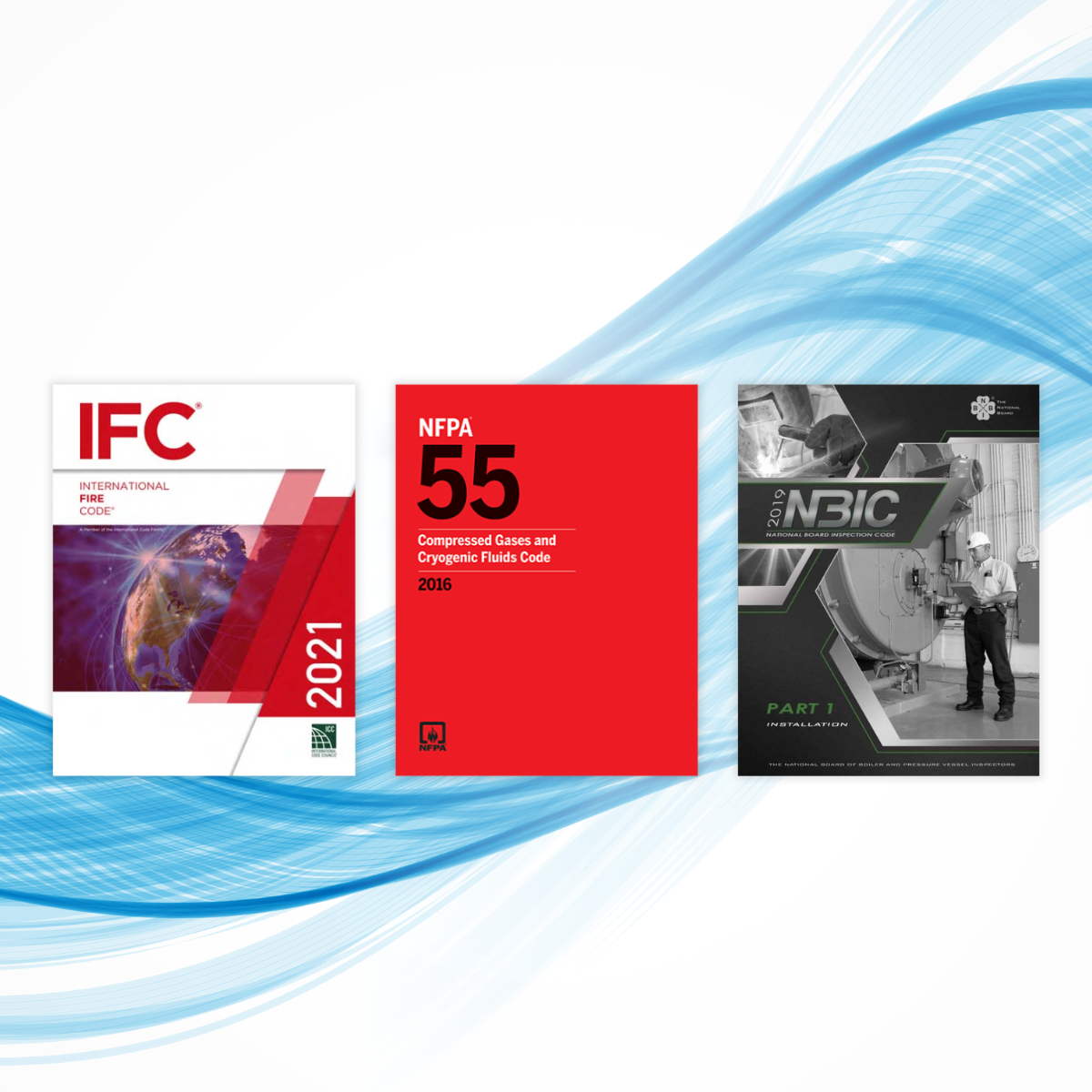
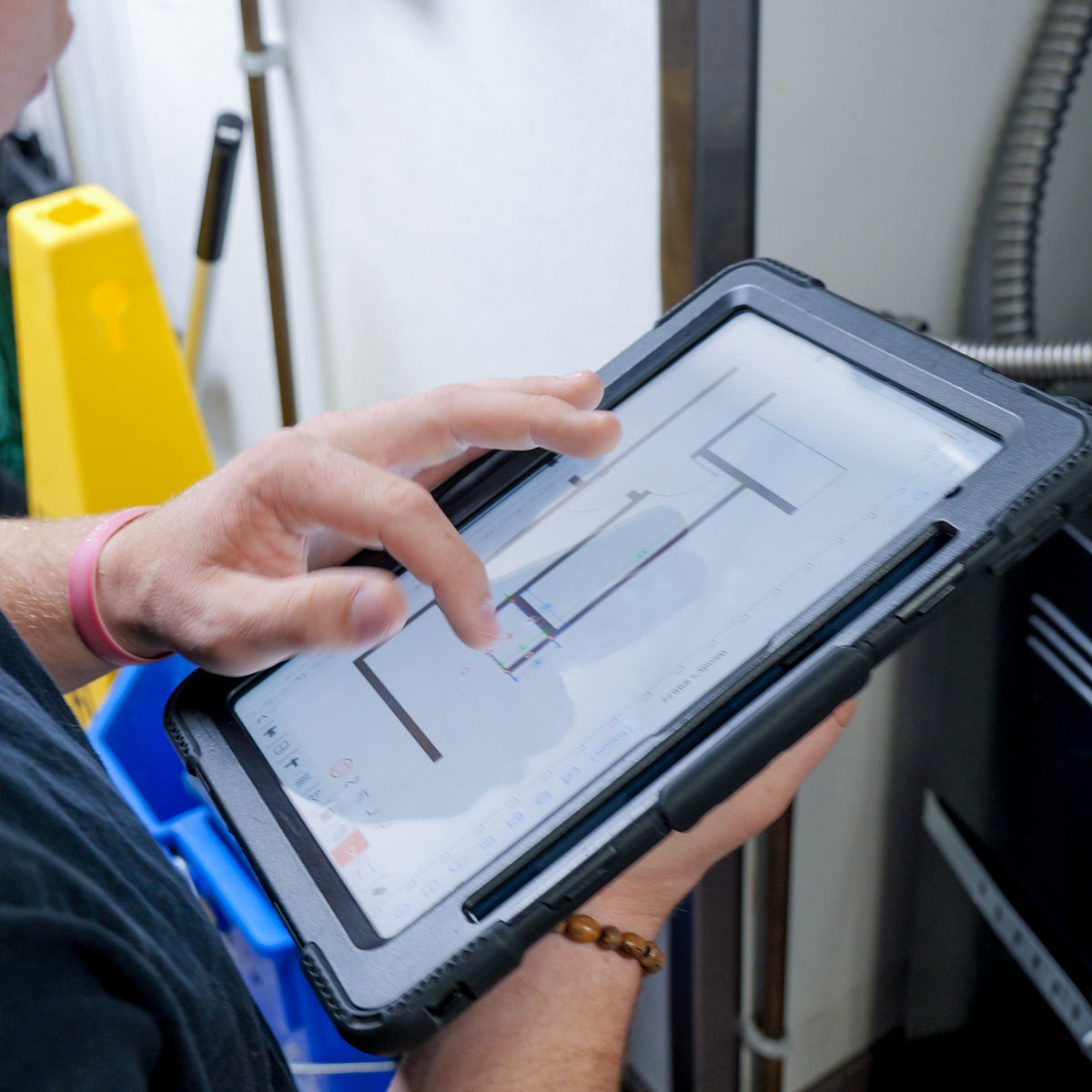
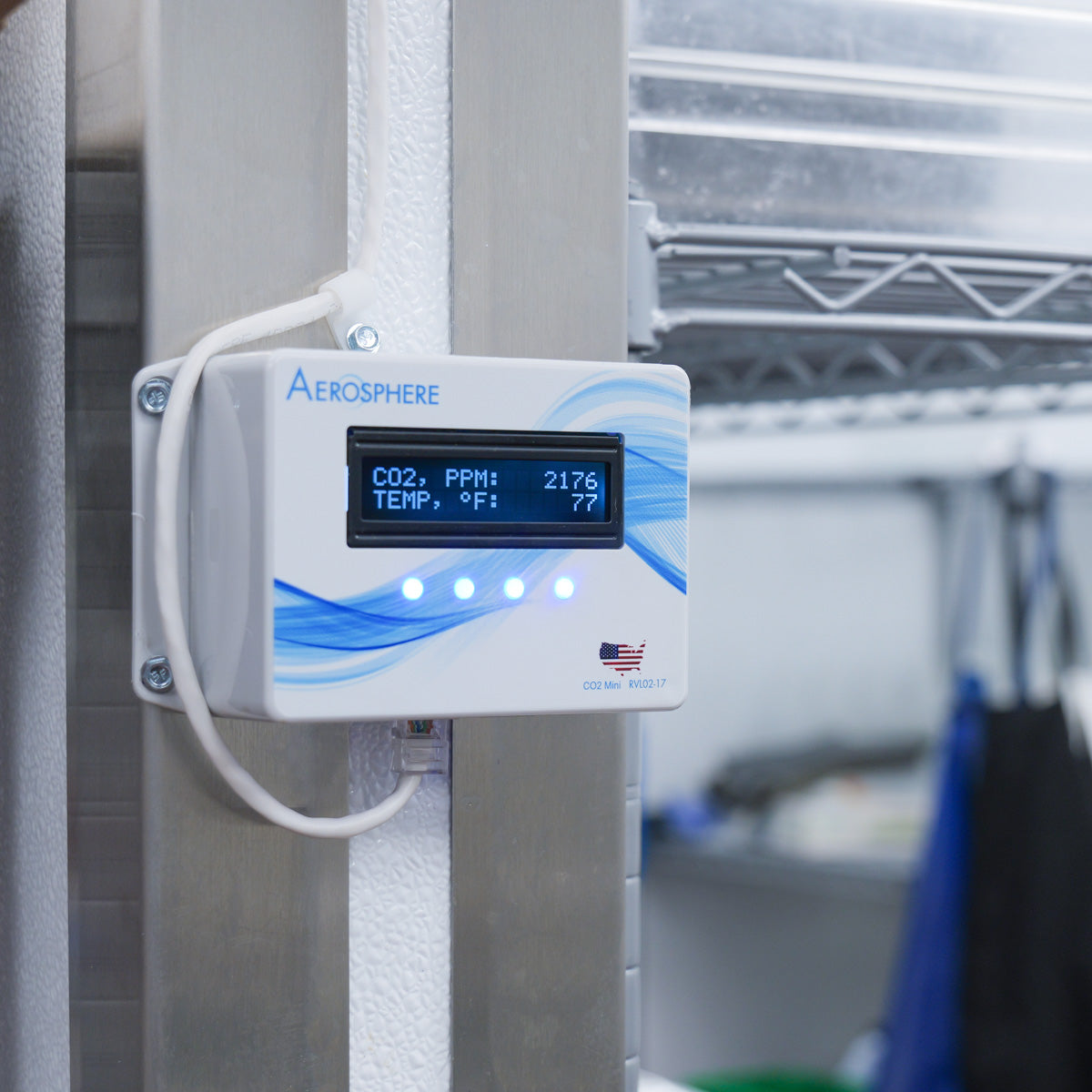
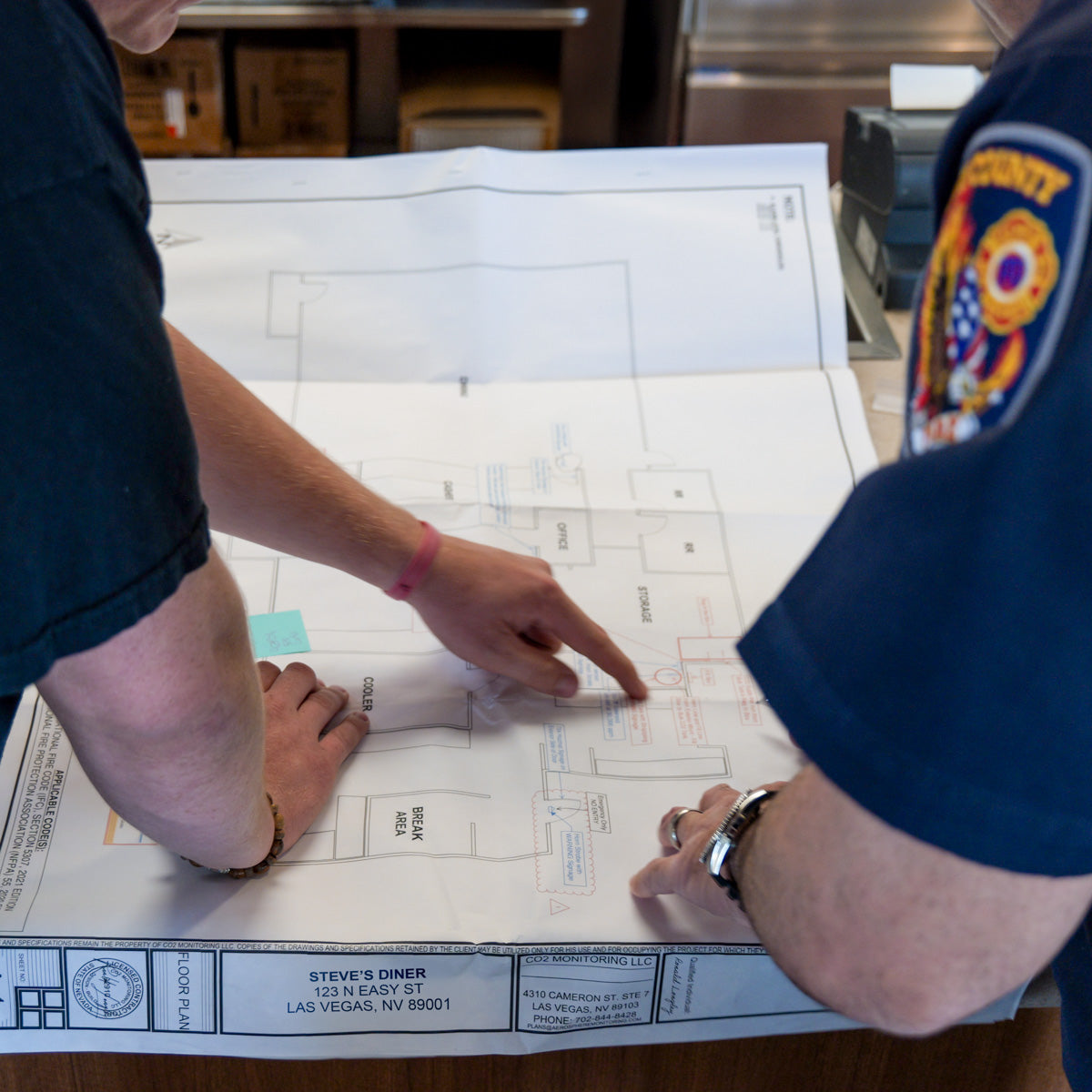
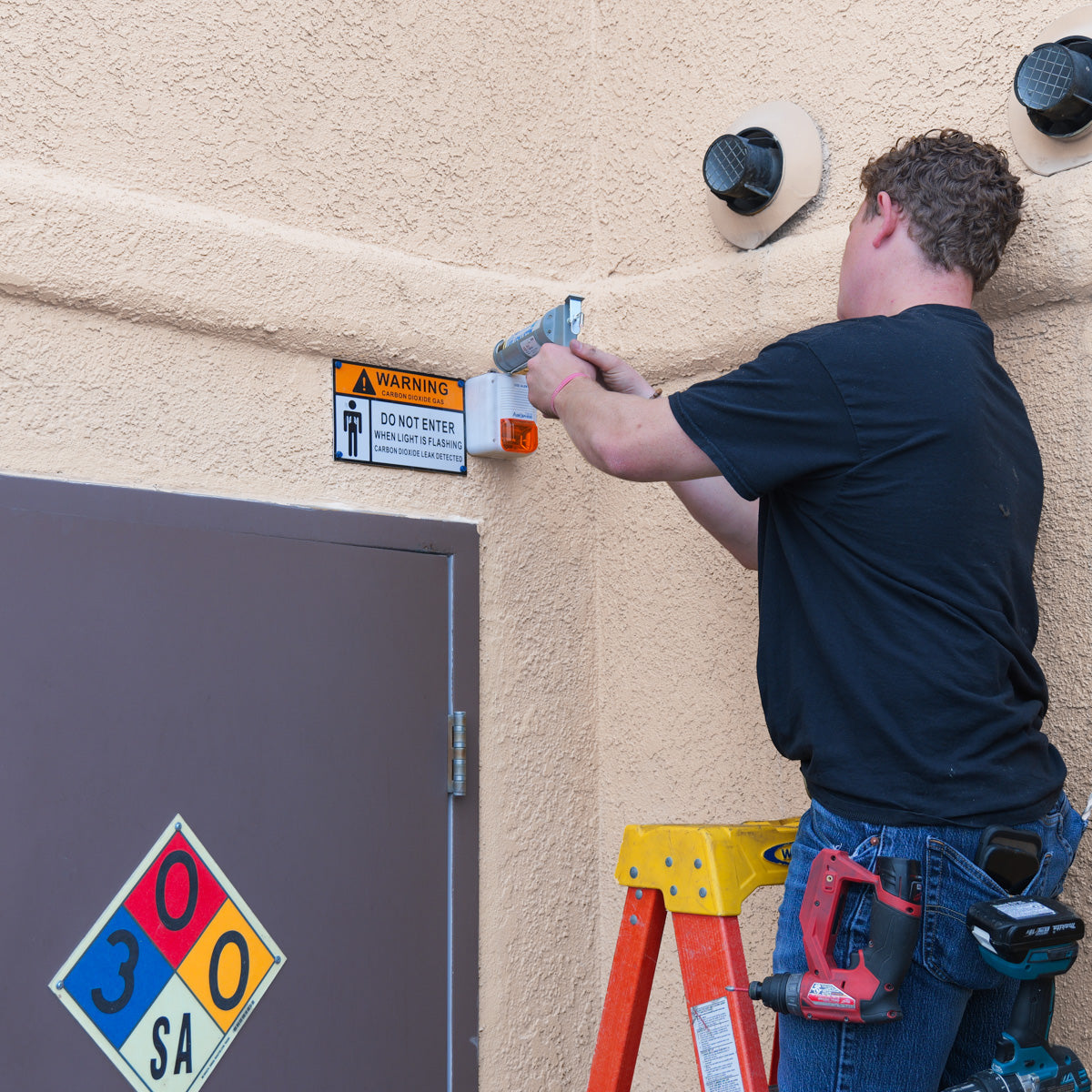

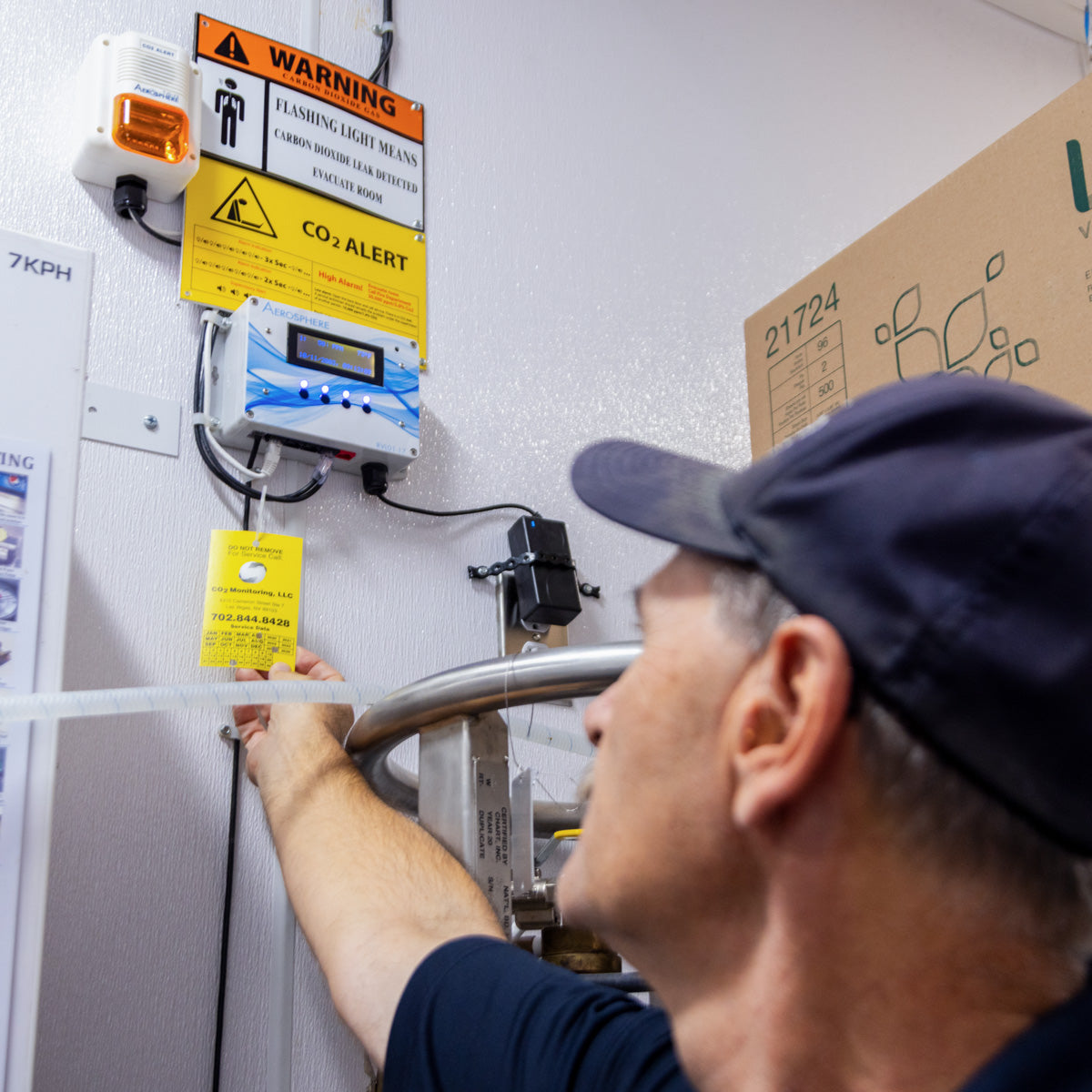
Step 1: Free CO2 Permit Diagnosis
Getting started with compliance shouldn't feel like guesswork. That’s why we offer complimentary permitting research based on just your business address. We'll explain how local enforcement works and identify what specific permits you need, whether it's fire, hazmat, or building.
As one of the most trusted names in CO2 compliance, we understand the fine print behind IFC (International Fire Code), NFPA 55, and NBIC (National Board Inspection Code). These codes are complex and vary in enforcement from state to state, but our job is to help you navigate them confidently.
We don’t just interpret regulations. We know how they're actually enforced and what inspectors are really looking for.
Get started by submitting our Free CO2 Permit Diagnosis Form.
Step 2: Site Survey & Compliance Assessment
Once we understand your jurisdiction's requirements, we conduct a site survey, especially if existing floor plans are outdated or unavailable. Our trained technician will:
- Document existing monitoring equipment (compliant and non-compliant) if any
- Evaluate alarm placement, ventilation systems, and signage
- Identify gaps in current compliance
- Draft a new digital floor plan aligned with permit requirements
This on-site inspection is crucial for accurate project estimating and also helps us preempt any potential issues before installation or inspection.
Step 3: Estimation & Equipment Specification
Our estimates are built around what’s required. Nothing more, nothing less. We never upsell unnecessary components. Instead, we take the data gathered from your site survey and match it against permit regulations to create a detailed, honest quote.
We manufacture our entire line of Aerosphere® CO2 Monitoring & CO2 gas management technologies in-house at our ISO-9001 certified facility in Las Vegas, Nevada. Our Aerosphere® product line includes:
- Single-zone monitors for small commercial settings
- Multi-zone monitoring systems for larger footprints
- Cloud-connected technologies with real-time data access across locations
- Fail-safe integrations including solenoid shutoff valves, which automatically cut CO2 gas flow in the event of a detected leak or alarm trigger, an increasingly required component
These variety of solutions mean we can support everything from a single franchise store to a nationwide chain.
Step 4: Drafting & Permit Application
Once you approve your quote, our drafting department steps in. Working alongside our estimators, they:
- Redraw detailed floor plans tailored to your site and local code
- Prepare supporting documents like product spec sheets and hazmat forms
- Complete and submit all permit applications to local authorities
If specialty applications are needed, like those in California (CERS) or for hazardous material storage, we handle those too. It’s all included.
Our drafting ensures that what’s on your permit application matches what’s physically feasible on-site.
Step 5: Installation & Scheduling
After permit approval, we coordinate the installation with your site contact to avoid downtime or disruption. Our technicians:
- Install all monitoring and alarm systems
- Install additional equipment (i.e., solenoid valves, battery backups, tank cages, and other associated equipment)
- Interface with HVAC or fire system contractors if integration is needed
We also work with any contractors you’ve already hired, including gas suppliers or GCs.
Our goal is a seamless, one-shot installation, done right the first time.
Step 6: Final Inspection & Fire Sign-Off
Once installation is complete, we’ll schedule and attend the final inspection with the AHJ (Authority Having Jurisdiction), usually a fire or building inspector. We make sure:
- All equipment matches what was submitted on the approved permit
- Placement of tanks, signage, alarms, and cabling meets specs
- CO2 gas detection system tested by CO2 test on-site in the inspector’s presence.
This step completes the compliance process, ensuring your business can open or continue operating without disruption to your CO2 systems.
Step 7: Annual Recertification & Service Renewals
For clients who opt into our recertification program, we return yearly to:
- Test and validate that all equipment functions correctly
- Tag your system with updated service tag
- Provide documentation showing your system passed renewal to the appropriate AHJ (if required)
If issues are found, we’ll send you a repair quote based on your original permit specs. We’ll keep you up-to-date with code requirements.
Modular Service Options
Not every client needs the full pipeline. Our services are available à la carte, including:
- CO2 system design and permit submission assistance
- Large-scale CO2 efficiency and safety consulting
- Final inspection coordination for your CO2 permits with necessary personnel
- Support and sourcing for third-party CO2 monitoring equipment
Custom pricing is available for partial project scopes.
At CO2 Monitoring, LLC, we provide full-service compliance solutions for CO2 safety—covering everything from initial research and permitting to final inspection and ongoing maintenance. Whether you're opening a new location, upgrading an existing system, or addressing a code enforcement notice, our experienced team is here to guide you every step of the way.
Nationwide Support with Local Roots
We maintain a strong regional presence with in-field technicians based in key service areas, including:
- Arizona
- California
- Colorado
- Nevada
- Utah
This local reach allows for faster site visits, reduced lead times, and better coordination with jurisdictional authorities in areas where permitting and inspection requirements can be especially complex.
Beyond our core service zones, we also operate nationally through our internal travel technician team—ensuring that no matter where your business is located, expert support is always within reach.
Whether you're managing a single facility or a nationwide portfolio, our team delivers consistent, code-compliant CO2 monitoring solutions across the U.S.